Технологические стадии окраски порошковыми материалами
Подготовка поверхности изделий Нанесение порошковых покрытий в электростатическом поле Формирование покрытий в печахПодготовка поверхности изделий
Подготовка поверхности изделий перед нанесением порошкового слоя обеспечивает необходимые адгезионные свойства оплавленного покрытия с поверхностью изделия и требуемые его качества. Существуют механические и химические методы подготовки поверхности.
Механическая подготовка поверхности
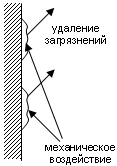
Заключается в механическом воздействии на материал поверхности изделия. При этом может удаляться окалина после сварки, шлифоваться поверхность. Механическое воздействие осуществляется с помощью:
- дробеструйных аппаратов;
- зачистки абразивными материалами;
- галтовочных аппаратов и т.д.
При механическом воздействии происходит передача энергии поверхностному слою обрабатываемого материала, то есть осуществляется активация поверхности. При этом адгезионные характеристики материала улучшаются. Однако эти свойства с течением времени исчезают. Поэтому задержка в нанесении порошкового слоя после механической обработки должна быть минимально возможной.
Химическая подготовка поверхности
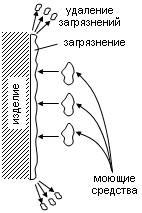
Заключается в химическом воздействии реагентов на поверхность изделий. Выбор необходимой технологии подготовки поверхности зависит от условий и срока эксплуатации изделий, от материала, из которого изготовлено изделие, а также от материала порошкового покрытия. Под технологией понимается последовательность и время операций воздействия химических реагентов.
В процессе подготовки изделий к покраске осуществляется очистка их поверхности от загрязнений (в основном масляных) с помощью моющих растворов и создание на поверхности изделий тонкого конверсионного слоя, обеспечивающего высокую адгезию и дополнительную антикоррозийную защиту. Для черных металлов конверсионный слой образуется при обработке фосфатными веществами, для цветных металлов - хроматными.
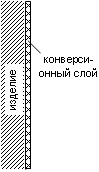
Кристаллические фосфатные слои обеспечивают высокие защитные свойства на поверхности стальных изделий, но они требуют многостадийную (более шести) обработку изделий. Аморфное фосфатирование обеспечивается при меньшем числе стадий, но подготовка поверхности при этом позволяет эксплуатировать изделия только в нежестких условиях эксплуатации (например, в помещениях).
Наилучшие результаты при обработке изделий из алюминия достигаются при воздействии соединениями с шестивалентным хромом. При этом, однако, увеличивается количество стадий и усложняется утилизация отходов. Поэтому во многих случаях применяется облегченная обработка трехвалентным хромом, дающим несколько худшие результаты.
Процесс нанесения порошкового покрытия
C помощью распылительного оборудования осуществляется нанесение слоя частиц на поверхность изделия. При этом должна обеспечиваться высокая эффективность осаждения порошка на изделие, требуемая толщина и равномерность слоя по всей поверхности, а также возможность окрашивания заэкранированных частей изделия.
Основные стадии процесса нанесения порошкового слоя:
- забор порошкового материала из насыпного или кипящего слоя с помощью эжекторного насоса,
- пневматическая транспортировка порошкового материала по шлангу от эжекторного насоса к распылителю,
- зарядка частиц порошкового материала зарядными устройствами распылителей,
- осаждение частиц порошка на изделие с образованием сплошного порошкового слоя.
Забор порошкового материала из бункеров с кипящим слоем целесообразно использовать при больших производственных программах или при окраске только одним цветом. Забор порошка из насыпного слоя ("забор из коробки") предпочтительнее применять при небольших производственных программах и частой смене цвета порошкового материала.
Зарядка частиц порошкового материала может осуществляться электростатическим или трибостатическим способами. При электростатическом способе зарядки частицы заряжаются ионами в поле коронного разряда, создаваемом высоковольтными электродами распылителя, что обеспечивает эффективную зарядку любых типов порошковых материалов. Трибостатическая зарядка осуществляется за счет трения порошкового материала о трибоэлектризующие конструкции распылителя. В конструкции распылителей при этом отсутствуют высоковольтные элементы, но зарядка при этом более чувствительна к степени осушки воздуха от влаги и к типам применяемых порошковых материалов.
При осаждении порошкового материала на изделие частицы проходят две зоны. Первая зона - это основной промежуток между распылителем и изделием. Здесь частицы порошка движутся в основном за счет потока воздуха по направлению к окрашиваемому участку поверхности изделия. Вторая зона - это узкий слой у поверхности изделия, где частицы порошка движутся в потоке воздуха, обтекающем изделие. Осаждение заряженных частиц порошка на поверхность изделия происходит под действием электрического поля. При образовании на поверхности изделия сплошного слоя порошка в нем начинают происходить процессы, препятствующие дальнейшему осаждению частиц на поверхность изделия. Таким образом, существует предельная толщина получаемого порошкового слоя, зависящая от величины заряда частиц в слое. Чем больше заряд, тем меньше предельная толщина слоя порошка.
При нанесении порошкового слоя на изделия сложной формы есть ряд особенностей в выборе режимов работы распылительного оборудования.
Процесс нанесения порошкового слоя на изделия осуществляется в установках нанесения покрытий, состоящих из окрасочных камер и систем рекуперации порошка.
Процесс формирования покрытия
В процессе формирования покрытия из нанесенного порошкового слоя создается монолитное качественное покрытие на поверхности изделия.Чаще всего процесс формирования покрытия осуществляется путем нагрева порошкового слоя до состояния его оплавления с образованием монолитного слоя. При последующей обработке в результате отверждения (для термореактивных материалов) или охлаждения (для термопластичных материалов) слоя образуется твердая пленка.
Процесс оплавления проходит в несколько стадий:
- сначала порошок проходит вязко-текучее состояние;
- затем проходит сплавление частиц порошка с образованием монолитного слоя;
- одновременно со сплавлением происходит смачивание покрываемой поверхности и растекание расплава полимера;
- на конечной стадии происходит удаление из расплавов газовых включений, то есть воздуха, находившегося в порах и между частицами порошка в слое, и газов, образующихся при деструкции полимера. Так как удаление газов осуществляется благодаря диффузии через расплав полимера, то для этого требуется довольно длительное время, соизмеримое со временем сплавления частиц порошка.
Процесс отверждения.
Отверждение покрытий на основе термореактивных материалов происходит в процессе теплового воздействия и длится вполне определенное время. Каждому покрываемому изделию соответствует оптимальный режим отверждения. Охлаждение покрытий на основе термореактивных материалов не влияет на свойства покрытия. Для термопластов режим и среда охлаждения во многом определяют качество покрытия. В качестве охлаждающего агента используют воду, минеральные масла, применяют охлаждение на воздухе.
Для формирования покрытия используют:
- конвективную теплопередачу тепла от нагретого воздуха к изделию с порошковым слоем (конвективные печи). Оплавление порошкового слоя происходит с внешней стороны, что затрудняет выход газов из слоя. Данный способ обладает большой универсальностью и не зависит от формы изделия, но имеет повышенные энергетические затраты;
- инфракрасный нагрев изделия с порошковым слоем. Оплавление порошкового слоя происходит с внутренней стороны, что облегчает выход газов из слоя. Способ обладает низкими энергетическими затратами, но пригоден для изделий простой конфигурации.
Поставлено и запущено в работу оборудование для получения двухслойной эпоксидной изоляции стальных труб диаметром до 820 мм. >>